WHY FINISHES FOR ALUMINUM PRODUCTS ARE IMPORTANT
If left untreated, aluminum will corrode! An ugly, whitish-gray powdery coating will appear (aka oxidation). And it’s not pretty. Therefore, aluminum warrants a proper finish. Aluminum finishes for architectural applications include mechanical, chemical, anodized, and organic coatings.
mechanical finish
Mechanical finishes are processes that physically change the surface via grinding and polishing. Thus, aluminum applications with mechanical finishes are in storefronts and trim, wall corner guards, exterior panels, infill railings, handrail posts, etc. Mechanical finishes entail buffing, directional textured, non-directional textured, and patterned.
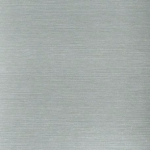
Buffing is the brightest mechanical finish as it creates a mirror reflectivity. Directional textured generates limited reflectivity but with a smooth, guiding, satin polish. Contrary, non-directional textured creates a matte finish of varying degrees of roughness through blasting. (Blasting method includes sand blasting, shot blasting, and glass-bead blasting.) Finally, patterned finishes are embossed or coined (sheet) metal. Embossing imprints both sides of the sheet aluminum, while coining refers to one sided stamping. Both typically require thin sheets.
CHEMICAL FINISH
Chemical finishes modify the surface of aluminum through one or more solutions. The main reasons for using a chemical finish, besides its cost effectiveness, are: to clean the surface to remove soils for a future finish; to prepare for anodizing (by producing an even electrochemical reactive surface); and to etch the surface to achieve a specific reflectivity. Etched chemical finishes on aluminum include matte finish, bright finish, and conversion coatings.
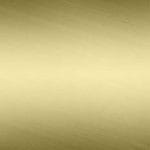
Matte finishes standards are fine matte, medium matte, and coarse matte. These etching treatments produce several degrees of mattes. Bright finishes are obtained by chemical brightening or electro polishing. Hence, chemical brightening treatments produce a high surface luster. Perfect for the fresh, shiny look!
Conversion coatings are used as the base for an organic coating. This is to prepare aluminum for coating (painting) or for an adhesive. However, conversion coatings are used as a post-treatment coating on other plating finishes, too.
ANODIZED FINISH
Anodizing is a very common finish in aluminum finishes for architectural applications. It’s an electrochemical process that replicates naturally occurring oxidation by providing a protective “metallic” film on the aluminum surface. Anodic coatings include clear, color, integral color, brite dip, and electrolytically deposited. Classifications designate them as Architectural Class I Coatings and Architectural Class II Coatings.
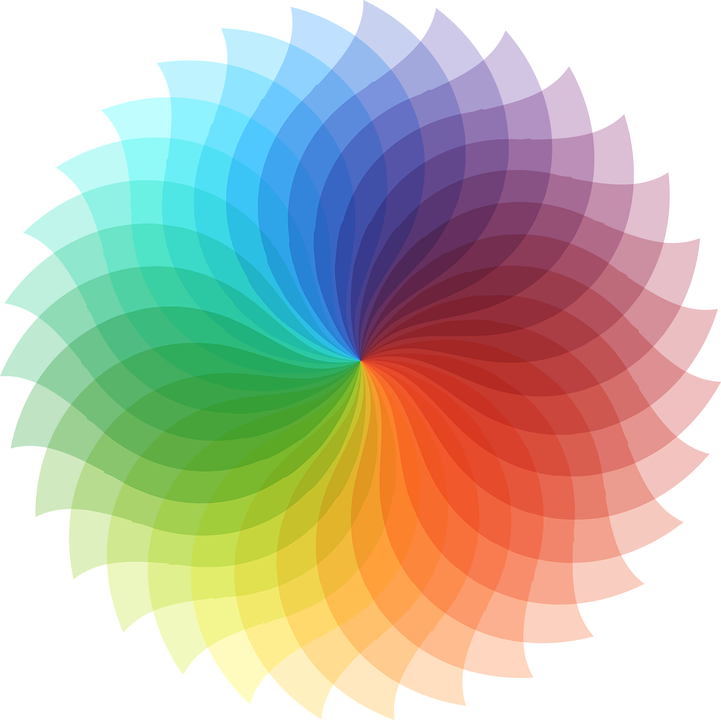
Class I anodize coatings have a mil thickness of 0.7 (18 microns) or greater. This coating is a high performance anodic finish. Class I is in exterior building products and misc. metals. These products include guardrails, fences, perforated railings, rain screens, curtain wall panels, and other building facades.
Class II anodize coatings have a minimum mil thickness of 0.4 (10 microns). Class II is suitable for interior items not subject to excessive wear and tear, such as column covers, wall fins, and radiator covers. Additionally, Class II coating are great for light exterior applications, such as beam wraps, post wraps, storefronts and trim.
ORGANIC COATINGS
In the architectural industry, “coating” is the preferred terminology over the word “paint.” Painting is, therefore, reserved to imply house paint and automotive paint. The many ways to apply organic coatings include brushing, spraying, flow coating, and dipping. Popular architectural coatings for aluminum include resinous, vitreous and laminate.
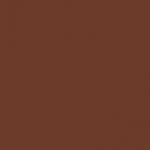
Resin-based coating, PVDF, is a fluoropolymer resin; abbreviation for polyvinylidene difluoride. Available for liquid and powder coatings, PVDF resin-based architectural coatings provide high-performance durability. These coatings are common in curtain wall panels, metal roofing, metal cladding, and other building facades because of high durability and resistance to chalking.
Vitreous enamel, also called porcelain enamel, is generally classified as porcelain enamels and includes enamels and ceramics. This coating provides a glassy, smooth, hard coating. Vitreous coatings are excellent in elevated temperatures because of its wear resistance and thermal, plus electrical insulation.
Laminated aluminum is manufactured by bonding a polyester film to the aluminum. This plastic film is available in a multitude of colors and results in very durable protection layer. In addition, you see these in cladding panels and glazing systems, mainly for its uniform, flat color and texture appearance.
Class II anodize coatings have a minimum mil thickness of 0.4 (10 microns). Class II is suitable for interior items not subject to excessive wear and tear, such as column covers, wall fins, and radiator covers. Additionally, Class II coating are great for light exterior applications, such as beam wraps, post wraps, storefronts and trim.
POWDER COATING
The main difference between liquid and powder coatings is the method of application. Equivalent paints are in both liquid and powder forms. Powder coating is a type of dry coating, while liquid coating goes on wet. For powder coating, electrostatically charged fine particles are first sprayed on aluminum, then cured under heat. This results in a remarkable thick coat with minimal or no paint running (unlike conventional liquid coatings).
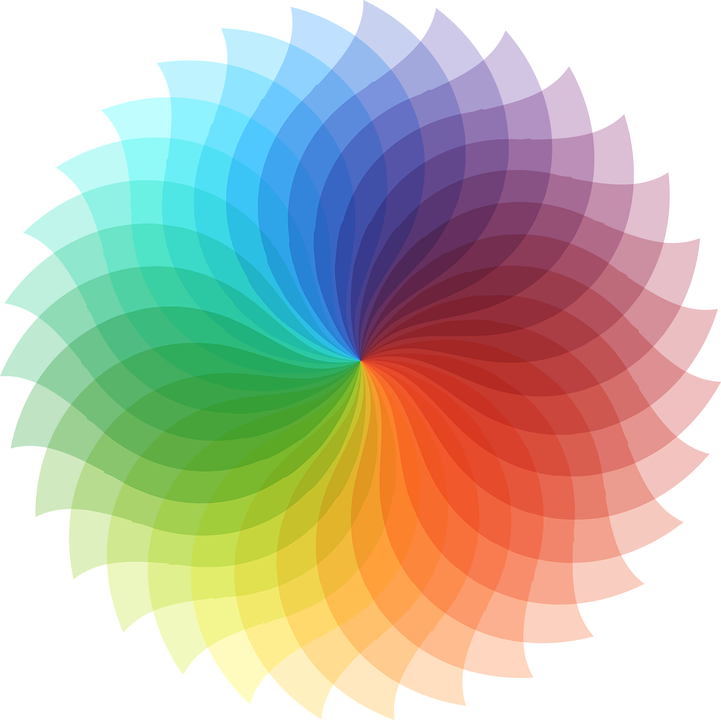
The architectural market in the construction industry has recently taken notice of powder coating and its many benefits and advantages. Plus, powder coating is environmentally friendly! The process does not use solvents or harmful fumes, unlike traditional liquid coatings. It also produces a superior finish in extreme weathering conditions. Besides the unlimited color selection, there are plenty of textures to choose from. Powder coating is commonly used on perforated panels to get an even coat between and around the holes.
Vitreous enamel, also called porcelain enamel, is generally classified as porcelain enamels and includes enamels and ceramics. This coating provides a glassy, smooth, hard coating. Vitreous coatings are excellent in elevated temperatures because of its wear resistance and thermal, plus electrical insulation.
Laminated aluminum is manufactured by bonding a polyester film to the aluminum. This plastic film is available in a multitude of colors and results in very durable protection layer. In addition, you see these in cladding panels and glazing systems, mainly for its uniform, flat color and texture appearance.
Class II anodize coatings have a minimum mil thickness of 0.4 (10 microns). Class II is suitable for interior items not subject to excessive wear and tear, such as column covers, wall fins, and radiator covers. Additionally, Class II coating are great for light exterior applications, such as beam wraps, post wraps, storefronts and trim.
SUBLIMATION COATING
Specialty finishes, such as sublimation, mimic marble, granite, wood, custom designs, etc. You will see these on commercial and residential aluminum products. Thus, these aluminum products include pergolas, canopies, sunscreens, railings, windowpanes, cladding, etc. Sublimation is the phase transition of a substance from a solid directly to a gas without going through a liquid phase. This occurs under an exact temperature and precise pressure conditions. This specialty finish, for instance, imprints a pattern; much like a tattoo.
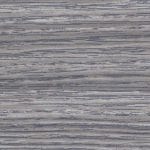
THE RIGHT ALUMINUM FINISHES FOR ARCHITECTURAL APPLICATIONS
An appropriate aluminum finish not only looks attractive, but improves performance in strength and sustainability. The specifications, desired appearance and application decide the best type of aluminum finishes for architectural applications. Therefore, architects and specifiers base this on personal taste, eco-friendliness, performance criteria, and cost.
Astro Metal Craft is a custom metal manufacturer. We have over 30 years’ experience in metal fabrication. Our core markets are Industrial Equipment/OEM’s and Architectural Metal Fabrication. Therefore, we are industry experts in both divisions and work primarily with stainless steel, aluminum, and Corten®. As always, if you have any questions, feel free to reach out to us. We love to help!